- zincdiecasting
- Apr 27, 2024
- 3 min read
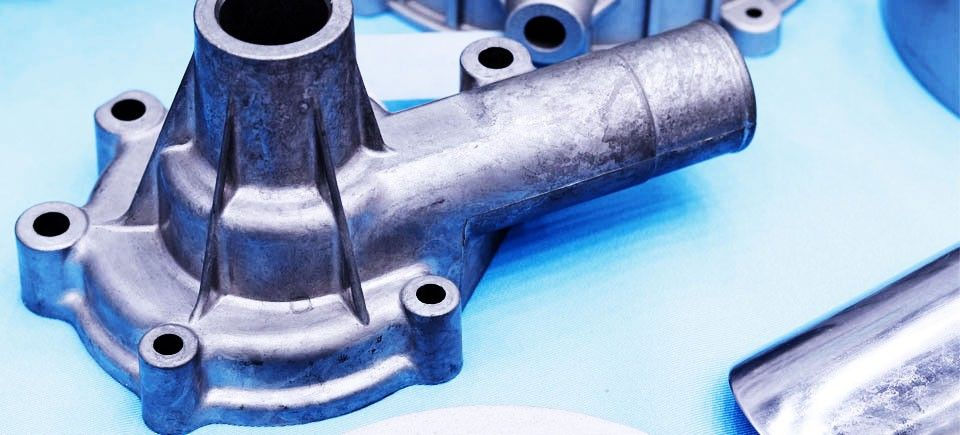
In the dynamic world of manufacturing, innovation is the lifeblood of progress. Nowhere is this more evident than in the realm of die casting, where precision, efficiency, and quality are paramount. China, long recognized as a manufacturing powerhouse, is at the forefront of this innovation, with mold manufacturers playing a crucial role in driving advancements in die casting technology. In this article, we take an in-depth look at how China's mold manufacturers are pushing the boundaries of innovation to redefine the die casting landscape.
The Evolution of Die Casting in China
Die casting has a rich history in China, dating back several decades. What started as a relatively rudimentary process has evolved into a sophisticated and highly efficient manufacturing technique, thanks in large part to continuous innovation driven by mold manufacturers.
In the early days, die casting molds were primarily made from conventional materials such as steel and aluminum. However, advancements in materials science and manufacturing techniques have paved the way for the development of more durable, heat-resistant, and cost-effective mold materials, such as high-strength steel alloys and ceramic composites.
Cutting-Edge Technologies and Techniques
At the heart of innovation in die casting are the cutting-edge technologies and techniques employed by mold manufacturers. From advanced CAD/CAM software for mold design to high-precision CNC machining equipment for mold fabrication, these technologies have revolutionized the way molds are created and optimized. Source Aluminum die Casting
One notable innovation is the use of additive manufacturing, or 3D printing, in mold making. This groundbreaking technology allows manufacturers to rapidly prototype and iterate on mold designs with unprecedented speed and precision, reducing time-to-market and enabling greater flexibility in design customization.
Enhanced Design Capabilities
Innovation in die casting extends beyond manufacturing techniques to include enhanced design capabilities. Mold manufacturers are leveraging advanced simulation software to optimize mold designs for improved performance, efficiency, and durability.
By simulating the casting process virtually, manufacturers can identify potential defects and inefficiencies early in the design phase, allowing for timely adjustments and optimizations. This not only minimizes costly rework and production delays but also ensures the quality and integrity of the final cast parts.
Focus on Sustainability and Efficiency
In today's increasingly environmentally conscious world, sustainability and efficiency have become key priorities for manufacturers. China's mold manufacturers are rising to the challenge by embracing eco-friendly practices and technologies that reduce waste, energy consumption, and environmental impact.
From implementing closed-loop cooling systems to recycling scrap materials, manufacturers are finding innovative ways to minimize their environmental footprint while maximizing efficiency and productivity. By embracing sustainability, they are not only reducing costs but also positioning themselves as responsible stewards of the environment.
Collaboration and Partnership
Innovation thrives on collaboration and partnership, and China's mold manufacturers are no exception. By working closely with customers, suppliers, and industry partners, manufacturers can gain valuable insights, access to new technologies, and opportunities for co-innovation.
Through collaborative efforts, manufacturers can tackle complex challenges, explore new market opportunities, and drive advancements in die casting technology. By fostering a culture of collaboration and partnership, China's mold manufacturers are paving the way for a brighter and more innovative future in die casting.
Looking Ahead: The Future of Die Casting in China
As China's mold manufacturers continue to push the boundaries of innovation, the future of die casting in China looks brighter than ever. With advancements in technology, materials, and design capabilities, manufacturers are poised to deliver even greater precision, efficiency, and quality in die cast parts.
From automotive and aerospace to electronics and consumer goods, the applications for die casting are vast and diverse. With innovation as their driving force, China's mold manufacturers are poised to play a leading role in shaping the future of die casting, driving progress and redefining excellence in manufacturing.
In conclusion, China's mold manufacturers are at the forefront of innovation in die casting, driving advancements in technology, materials, and design capabilities. Through cutting-edge technologies, enhanced design capabilities, and a focus on sustainability and collaboration, manufacturers are redefining the die casting landscape and shaping the future of manufacturing in China and beyond.